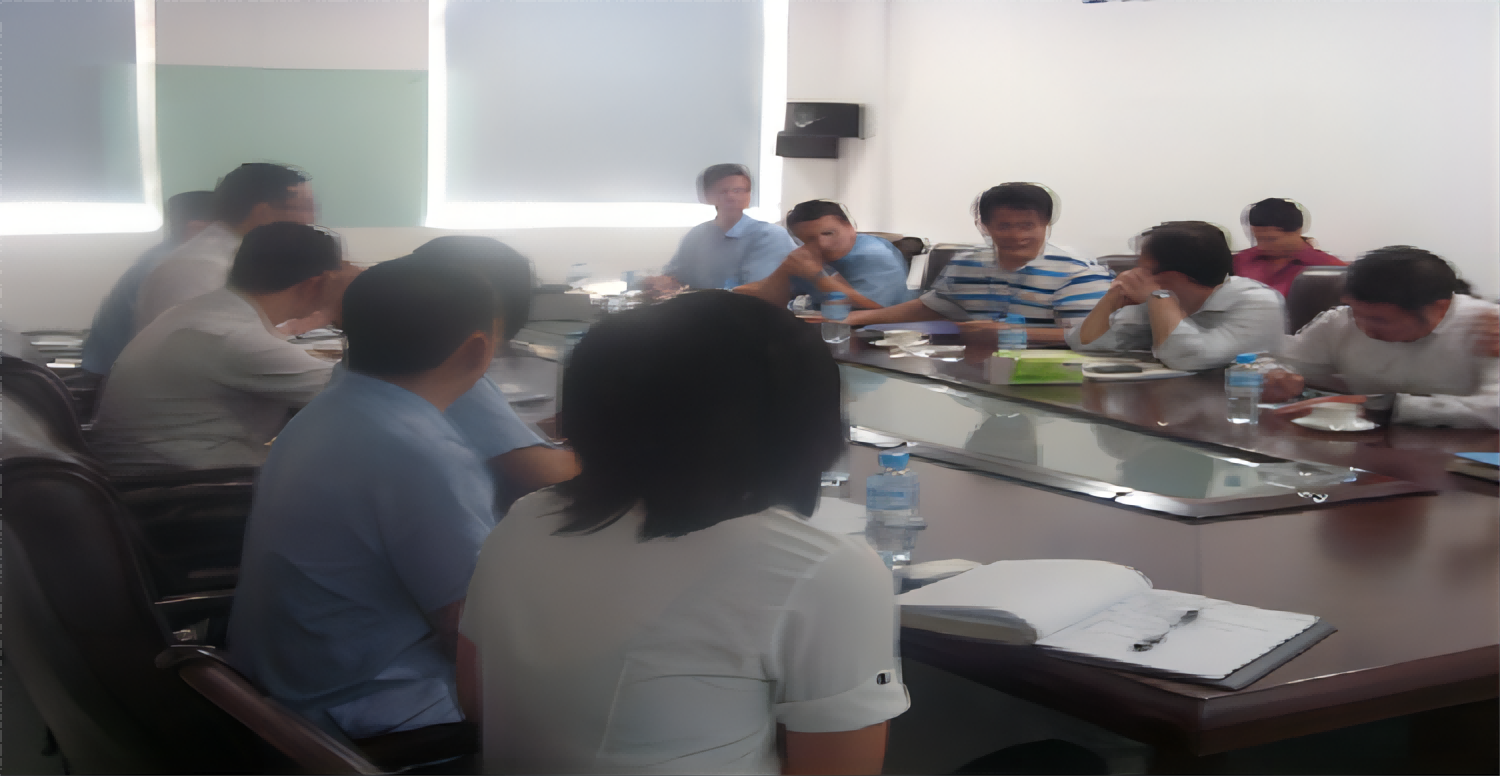
Employee Excellence
1) Adhering to the Quality Policy of "Quality as the Root, Reputation as the Foundation, Customer First, Continuous Improvement"
Continuously improve quality management with full participation and firmly establish the customer-first mindset. Always be responsible for product quality and provide customers with more refined and superior products and services.
2) Enhancing Manager Training and Improving the Quality Levels of All Managers
Use training, theoretical exams, and meeting questions to learn and advance knowledge and quality management skills. Focus on improving the quality knowledge and management levels of leaders at all levels and strengthen the sense of responsibility.
3) Promoting Full Employee Training to Achieve Comprehensive Quality Management Participation
Organize targeted quality training. Increase awareness among all employees about the importance of advancing the quality management system review work. Align thoughts and actions with the overall requirements of building a quality management system, enhancing the sense of urgency and responsibility. Strengthen employees' understanding of system documents so that everyone is clear about the quality policy and objectives and knows their quality inspection duties, laying a solid foundation for the effective operation of the quality system.
4) Strengthening the Layered Quality Management Responsibility System to Ensure Implementation of Responsibilities
Implement quality responsibility at every level from the company to departments, teams, and employees. In 2019, quality goals and indicators were broken down and assigned to each organization and position. The quality responsibility system must be established, decomposing and implementing quality responsibility across all processes, personnel, and departments involved in production. Through supervision, rewards, penalties, and accountability, ensure the effective operation of the responsibility system.
5) Continuously Conduct Internal Audits to Evaluate the Implementation Effectiveness of the System
2019 is a critical year for the implementation of the system. The Quality Department will conduct internal audits quarterly, using plans that include discussions, document reviews, record checks, and on-site inspections to find and address problems. Train key personnel to become qualified internal auditors to fulfill their duties carefully and thoroughly in daily work, achieving continuous improvement in the quality system.
6) Strictly Implement Corrective and Preventive Measures
Address non-conformities and observations identified in internal audits and inspections, tracking the effectiveness of corrections to continuously improve the quality management system. Each unit should identify risks in the production process and develop corresponding preventive measures, extending system operation from process control to proactive prevention.
7) Ongoing Quality Business Process Streamlining
All work is a process. Even the most complex tasks can be broken down into smaller processes. Understand the output requirements of each process, break it down using process methods, identify the input requirements, and develop control methods to be strictly implemented. Effective process management ensures zero defects in each business process, leading to zero defects in the overall company operation.
8) Improving Quality Cost Management
Encourage full participation in quality cost management with the aim of optimizing quality costs, fully implementing quality cost control, and achieving quality cost efficiency. Establish a quality improvement proposal system and reward those who contribute to reducing quality costs, enhancing employee motivation for quality improvement.
Establish suitable quality cost targets and clarify management responsibilities: Quality costs should be managed throughout the production process, involving all relevant departments. By integrating quality cost statistics and analysis into departmental quality functions, sustained quality cost management can be achieved. Strengthen goal orientation and responsibility management in quality cost management.
9) Enhancing Monitoring and Measurement Capabilities
Gradually purchase monitoring and measurement equipment in phases according to importance, improving the company's capabilities. Establish management logs and usage registers for monitoring and measurement equipment, and create regular inspection plans. Maintain and service equipment, conduct Measurement System Analysis (MSA), and develop operation manuals for inspection equipment and tools.
10) Promoting Standardization of Inspector Positions
Standardize inspector roles from human resources, responsibilities, skills, and management requirements. Clarify inspector resource allocation and business activities, creating a systematic quality control and supervision system to improve manufacturing quality.
Promote operational standardization by detailing input/output requirements, steps, methods, standards, and responsibilities for all product realization processes. Develop clear, standardized, and easy-to-follow operational documents, focusing on periodic standard operations (for operators) and non-periodic standard operations (for maintenance workers, mold adjusters, etc.), along with inspection guides.
Continuously train inspectors based on identified product quality characteristics, control plans, and process requirements, improving their skill levels. Establish skill requirements and knowledge standards for inspectors, continuously enhancing their abilities. Remove non-compliant personnel and optimize the inspector team. Evaluate process outputs against established criteria, analyze causes for any deficiencies, implement corrective measures, and re-evaluate results. Ensure ongoing analysis and improvement according to corrective and preventive management procedures.
We should aim for "teamwork and quality breakthroughs," continuing to uphold the spirit of pragmatism, excellence, responsibility, and bold action. Let's embark on our new journey, contributing to our "enterprise dream."